For a globally deployed force, getting something in the right place at the right time can be challenging. The Air Force, for its part, is undertaking a variety of logistics initiatives to help ease that burden and make the force more lethal.
On a large-scale level, the Air Force is pursuing a worldwide logistics command-and-control network, because if “we are going to be an agile, responsible Air Force that can deliver multiple effects in multiple domains at a speed that overwhelms our adversary, we need logistics command and control to keep up with that,” Gen. Ellen Pawlikowksi, commander of Air Force Materiel Command, said during a keynote address at the Air Force Association‘s annual conference on Sept. 18.
This will allow the force to have the visibility of where things are and where they need to be in a decentralized way, she said. That will give it the agility to be proactive, and enable the logistics support to be out in front of where operators need these things, she added.
This logistics command and control will be absolutely essential to link the different capabilities to the different to people to the different assets to provide the rapid response capability that a combatant commander will need, Pawlikowski explained.
RELATED
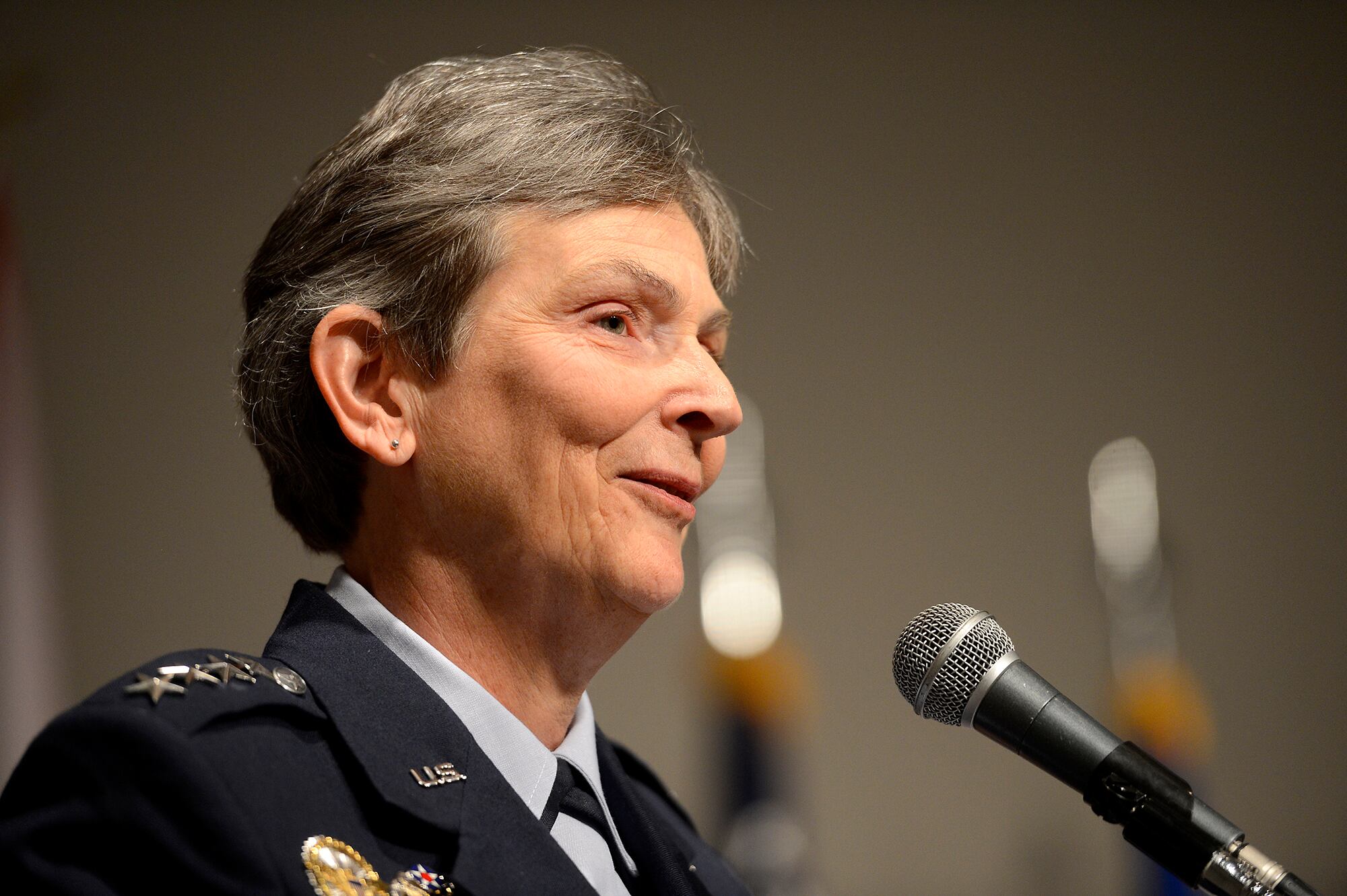
For example, the force must be able to respond to Gen. Terrence O’Shaughnessy, the commander of Pacific Air Forces and the air component commander for U.S. Pacific Command, who has to be able to fight tomorrow from an austere environment where he has not yet had time to set up the infrastructure.
Pawlikowski also acknowledged the Air Force can’t do this alone, but rather will require support from the industrial base, international partners and the joint force, such as Transportation Command.
In terms of specific initiatives to improve servicewide logistics, Pawlikowski explained that additive manufacturing is playing a large role. While she admitted the Air Force has been pursing this for some years and still has work to do, advancements in 3-D printing allow the force to not worry about the supplying and ordering of parts cutting out the supply chain and reducing timelines for making parts.
In a real-world example, she noted that the service had to replace load-bearing handles on C-5 aircraft for $1,600 each. The part, however, was unavailable, and the Defense Logistics Agency said it didn’t know when it would be able to get the part. Through 3-D printing, the service was able to produce the part for $300 and didn’t have to wait around for it to be delivered.
The next phase for the service in terms of additive manufacturing, Pawlikowski said, is mainstreaming the process, which means transitioning from plastic parts to metal. “Plastic works really well, but I don’t think I want [to] replace aircraft parts with a piece made out of plastic,” she said.
Additionally, the Air Force is pursuing something called conditioned-based maintenance as opposed to planned-depot maintenance, which involves maintenance based on schedules and timetables. The new approach will seek to get out in front of maintenance, looking at available data to predict where there is going to be failure, and eliminating that before it comes to a head.
Pawlikowski also mentioned how the Air Force is taking software development and sustainment seriously. As more and more systems become reliant on software — think the F-35 — maintaining and sustaining those software baselines and delivering patches in a timely manner will be critical.
Mark Pomerleau is a reporter for C4ISRNET, covering information warfare and cyberspace.