EVERETT, Wash. — Boeing’s KC-46 program manager has vowed to fix a critical technical issue before delivery of the first tanker this summer, and a fix appears to be within grasp, he told reporters Thursday.
The U.S. Air Force may not accept the first KC-46 tanker until it reverses a category-1 deficiency — the designation for the most serious technical issue — involving the remote vision system. The RVS is a series of cameras and sensors made by Rockwell Collins that allows the boom operator to guide the boom into an aircraft’s refueling receptacle.
That system needed some fine-tuning for use in certain times of day where the sun is at particular angles, creating shadows and glare that make it difficult to insert the boom without it scraping the receiver aircraft, said Mike Gibbons, Boeing’s program manager.
But a software fix is undergoing flight testing, and Gibbons expects the Air Force to declare the issue resolved in the next couple of months, he told reporters touring the company’s production facilities in Everett, Washington.
“We worked an enhancement, and what we were able to do through software is sharpen the image and the shadows get rid of the glare. We actually flew that for the first time in mid-March with the Air Force on board. So they looked at it; they provided some additional commentary,” he said.
RELATED
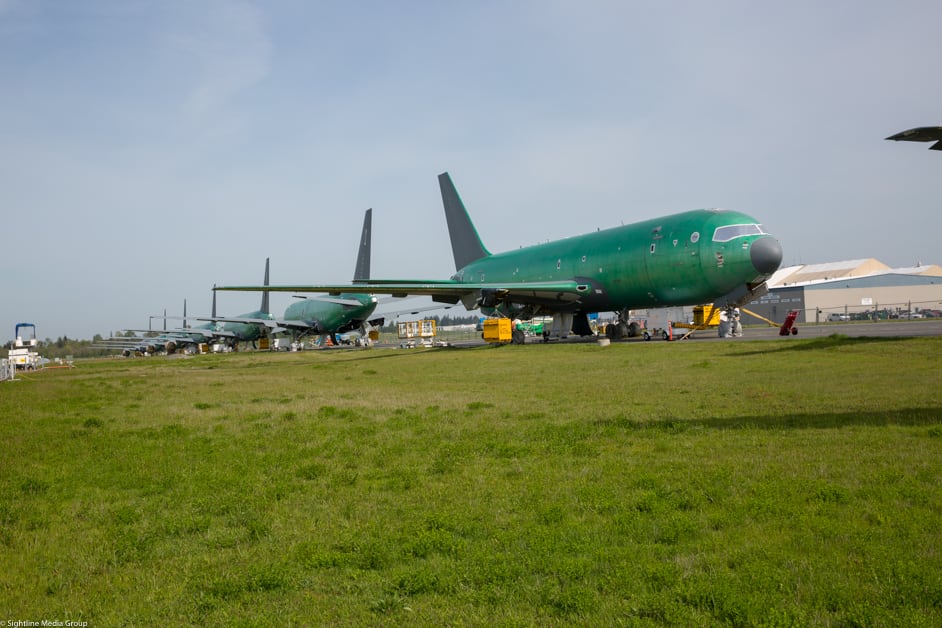
Boeing’s four test KC-46 aircraft are now flying with the second iteration of the software, and that version will be used during final tests of the RVS over the next month. Boeing officials are confident the RVS deficiency will be downgraded to a category-2 problem, if not eliminated altogether, he added.
That will allow the company to deliver the first tanker as early as sometime this summer, according to Boeing’s schedule.
The RVS problem is connected to another open category-1 deficiency for “undetected contacts outside the receptacle,” more commonly referred to as the KC-46’s boom-scraping issue.

Last September, the Air Force grew concerned that the KC-46 had a higher rate of incidents where the boom had hit outside a receiver plane’s receptacle, scraping the surface of that aircraft — a significant and potentially expensive complication for stealth jets that rely on radar-absorbent coatings to maintain low observability.
Boeing in November 2017 brought in Tom Russell, the director of remote sensing for its satellite systems business, to help guide improvements to the RVS and boom operator station.
The company and the Air Force also collected data from the KC-46 test fleet and compared it to the rate of “undetected contacts” throughout the service’s tanker fleet, which today is comprised of KC-135 and KC-10 tankers.
“What we determined is, the KC-46 is well within the family,” Gibbons said. “We have had contacts outside the receptacle; so do legacy tankers. Our rate is within the norm for what we’re seeing out in the fleet today.”
For that reason, Boeing has decided to concentrate on the RVS problem, believing that if it can improve that system, the rate of undetected contacts would naturally decrease — allowing the Air Force to close out the RVS and undetected contact deficiencies simultaneously.
The Air Force, naturally, has a different point of view. It hasn’t seen the final version of Boeing’s assessment, Air Force officials told reporters May 9. But the key problem isn’t necessarily the scraping. It’s that the scraping is undetected by the boom operator and therefore not conveyed to the receiver aircraft’s crew.
“We’re not focused on counting scratches. We’re trying to think more about performance in general,” one Air Force official said. “If a contact occurs, it should be reported. Therefore, there should be zero [undetected contacts of the receptacle].”
Unlike the KC-135 and KC-10, where boom operators sit (or in the KC-135’s case, lay down) in a pod near the back of the tanker and look out a window as they guide the boom toward a receiver aircraft, KC-46 boom operators sit in a station at the front of the plane, close to the cockpit.
With no windows to look out, KC-46 boom operators are completely dependent on the aircraft’s seven cameras — three panoramic cameras and four boom cameras — which provide electro-optical and thermal imagery in a stereoscopic display. For that reason, the visual acuity of the RVS is critical to the success of the boom operator being able to complete tasks efficiently and safely.
Russell said Boeing has made three major enhancements to the RVS:
- Make it more intuitive for the operator to adjust the camera settings.
- Provide “real-time” tools that tell the operator how they can augment image quality in certain weather or lighting conditions.
- Retune the camera system to improve imaging when the light is at certain angles.
Sean Martin, the company’s chief air-refueling operator and a former KC-135 boom operator for the Air Force, emphasized that the RVS produces clear imagery most of the time.
“It’s easy for this discussion to sound like we’re totally reinventing our cameras and we’re out there trying to solve a really difficult problem. What we’re talking about, its probably in the area of about 5 to 8 percent of all of the aerial refueling we do,” he said.
Because Boeing is locked into a fixed-price contract that makes it responsible for paying any costs above the $4.9 billion award value, it has had to use its own funding to pay for improvements to the RVS. Gibbons declined to comment on how much the company is investing on the system.
However, Gibbons and Martin stressed that the Air Force’s original requirement for the system, written almost a decade ago, left much up to interpretation. For instance, the RVS requirement calls for a system with “sufficient visual acuity to be able to perform aerial refueling in all conditions,” a qualitative description that doesn’t lay out exact parameters.
The requirements also included no information on the acceptable number of undetected contacts, Gibbons said.

That may be why Leanne Caret, the head of Boeing’s defense business, said the company’s most significant lesson learned during the course of the program is that all parties need to make sure they’re on the same page in regard to requirements.
“How do you define the spec appropriately? How do you make certain from a verification and a validation perspective that the intent as well as the exactness of it is there?” she told reporters May 3.
One Air Force official pushed back on those criticisms, saying that operators have the latitude to write deficiency reports for poor performance during testing.
“Operators, as they’re going through flight tests, as we’re collecting all the test data, they can write a DR [deficiency report] if they have an overarching concern about what they’re seeing in flight tests,” the source said. “It doesn’t necessarily have to be tied exactly to a spec requirement.”
Fixing the centerline drogue issue
Boeing will contend with one other category-1 deficiency this summer: a problem with the centerline drogue system, or CDS.
The KC-46 is built with a mechanical lock on its CDS that will attach to a receiver aircraft and will release when tension between the tanker and the receiver exceeds a poundage rate in excess of 620 pounds, Gibbons said.
However, there have been cases when it unintentionally unlocks, such as when the tanker is flying at high speeds.
The problem can easily be rectified by refining the software that controls the tension of the drogue, but that entails gathering more flight data.
“There’s a simple fix here, and Boeing is going to fix it. It’s just [a matter of] when are we going to fix it,” Gibbons said. “We and the Air Force have agreed … for a while that the right time to do that is after we gather sufficient flight test information from some of these drogue contacts, go in and update the software, and then we’ll roll it in through the summer and test it out again.”
Valerie Insinna is Defense News' air warfare reporter. She previously worked the Navy/congressional beats for Defense Daily, which followed almost three years as a staff writer for National Defense Magazine. Prior to that, she worked as an editorial assistant for the Tokyo Shimbun’s Washington bureau.