WASHINGTON — Lockheed Martin’s F-35 Joint Strike Fighter is on the verge of full-rate production, with a decision slated for early 2021. But a congressional watchdog group is concerned that as the company ramps up F-35 production, its suppliers are falling behind.
And those supply chain problems could get even worse as Turkish defense manufacturers are pushed out of the program, the Government Accountability Office said in a May 12 report.
According to the GAO, the number of F-35 parts delivered late skyrocketed from less than 2,000 in August 2017 to upward of 10,000 in July 2019.
The number of parts shortages per month also climbed from 875 in July 2018 to more than 8,000 in July 2019. More than 60 percent of that sum was concentrated among 20 suppliers, it said.
RELATED
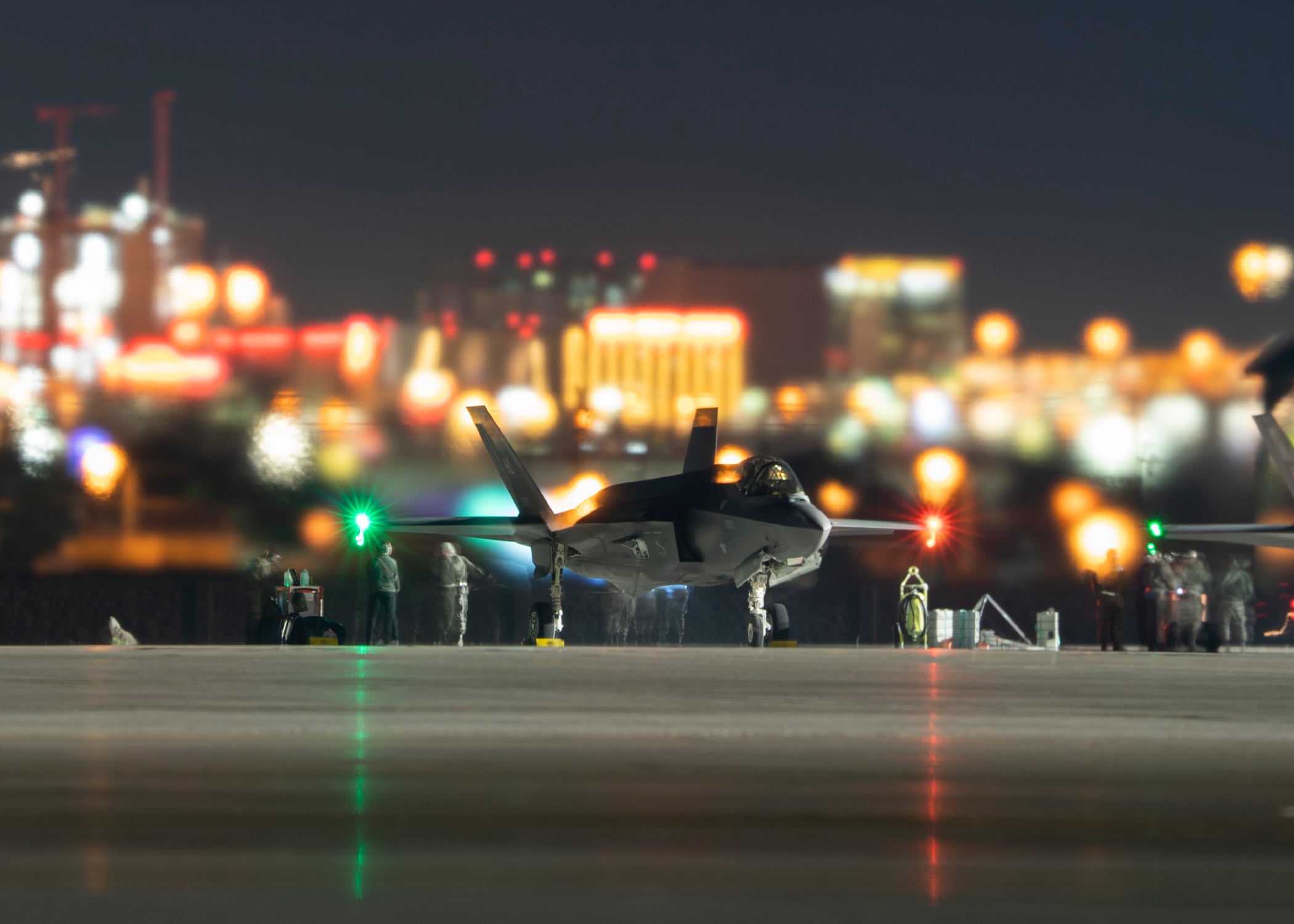
“To mitigate late deliveries and parts shortages — and deliver more aircraft on time — the airframe contractor has utilized methods such as reconfiguring the assembly line and moving planned work between different stations along the assembly line,” the GAO said.
“According to the program office, such steps can cause production to be less efficient, which, in turn, can increase the number of labor hours necessary to build each aircraft,” which then drives up cost, the GAO added.
Those problems could be compounded by Turkey’s expulsion from the F-35 program, which was announced last year after the country moved forward with buying the Russian S-400 air defense system. Although Turkey financially contributed to the development of the F-35 as a partner in the program, the U.S. Defense Department has maintained that Turkey cannot buy or operate the F-35 until it gives up the S-400.
The Pentagon has also taken action to begin stripping Turkish industry from the aircraft’s supply chain, a process that involves finding new companies to make 1,005 parts, some of which are sole-sourced by Turkish companies.
Ellen Lord, the Pentagon’s undersecretary for acquisition and sustainment, had hoped to stop contracting with Turkish suppliers by March 2020, but in January she said that some contracts would extend through the year, according to Defense One.
While the Defense Department has found new suppliers to manufacture the parts currently made in Turkey, it is uncertain whether the price of those components will be more expensive. Furthermore, as of December 2019, the new production rates for 15 components were lagging behind that of the legacy Turkish producers.
“According to program officials, some of these new parts suppliers will not be producing at the rate required until next year, as roughly 10 percent are new to the F-35 program,” the GAO said.
“Airframe contractor representatives stated it would take over a year to stand up these new suppliers, with lead times dependent on several factors, such as part complexity, quantity, and the supplier’s production maturity. In addition, these new suppliers are required to go through qualification and testing to ensure the design integrity for their parts.”
The F-35 Joint Program Office disagreed with the GAO’s recommendation to provide certain information to Congress ahead of the full-rate production decision, including an evaluation of production risks and a readiness assessment of the suppliers that are replacing Turkish companies.
In its statement, the JPO said it is already providing an acceptable number of updates on the program’s readiness for full-rate production.
Hard times for the F-35’s engine supplier
Not all F-35 production trends reported by the GAO were bad for the aircraft. Since 2016, Lockheed has made progress in delivering a greater proportion of F-35s on schedule, with 117 of 134 F-35s delivered on time in 2019.
However, one of the biggest subsystems of the F-35 — the F135 engine produced by Pratt & Whitney — drifted in the opposite direction, with a whopping 91 percent of engines delivered behind schedule.
At one point in 2019, Pratt & Whitney stopped deliveries of the F135 for an unspecified period due to test failures, which also contributed to the reduction of on-time deliveries.
According to the Defense Contracts Management Agency, “there have been 18 engine test failures in 2019, which is eight more than in 2018, each requiring disassembly and rework,” the GAO wrote. “To address this issue, the engine contractor has developed new tooling for the assembly line and has established a team to identify characteristics leading to the test failures. Plans are also in place for additional training for employees.”
Valerie Insinna is Defense News' air warfare reporter. She previously worked the Navy/congressional beats for Defense Daily, which followed almost three years as a staff writer for National Defense Magazine. Prior to that, she worked as an editorial assistant for the Tokyo Shimbun’s Washington bureau.