FORT WORTH, Texas — The F-35 fighter jet is the U.S. Defense Department’s largest and most expensive weapons program, with a projected life-cycle cost of more than $1 trillion.
That price tag makes it a huge moneymaker for prime contractor Lockheed Martin, but with big opportunity comes big responsibility to fix the various problems that have cropped up during the Joint Strike Fighter’s development. As Lockheed’s new general manager of the F-35 program, Greg Ulmer is the latest official charged with fixing those issues.
Defense News sat down with Ulmer in June for a wide-ranging interview about the F-35’s future and how Lockheed is addressing continued challenges in the program. Here are the four major points that the program head detailed:
1. Full-rate production
The F-35 flew its final developmental flight test in April, and after its initial operational test and evaluation period starting this fall — where the F-35 will be assessed by the Pentagon’s independent weapons tester — the department will make a decision about whether to move into full-rate production.
“We are positioned to support [full]-rate [production], which means all the tooling is in place, the training to equip and train the employees to do that work, the materials on order, the workflow through the factory in terms of our planning have been laid to support that,” Ulmer told Defense News in a June 22 interview.
RELATED
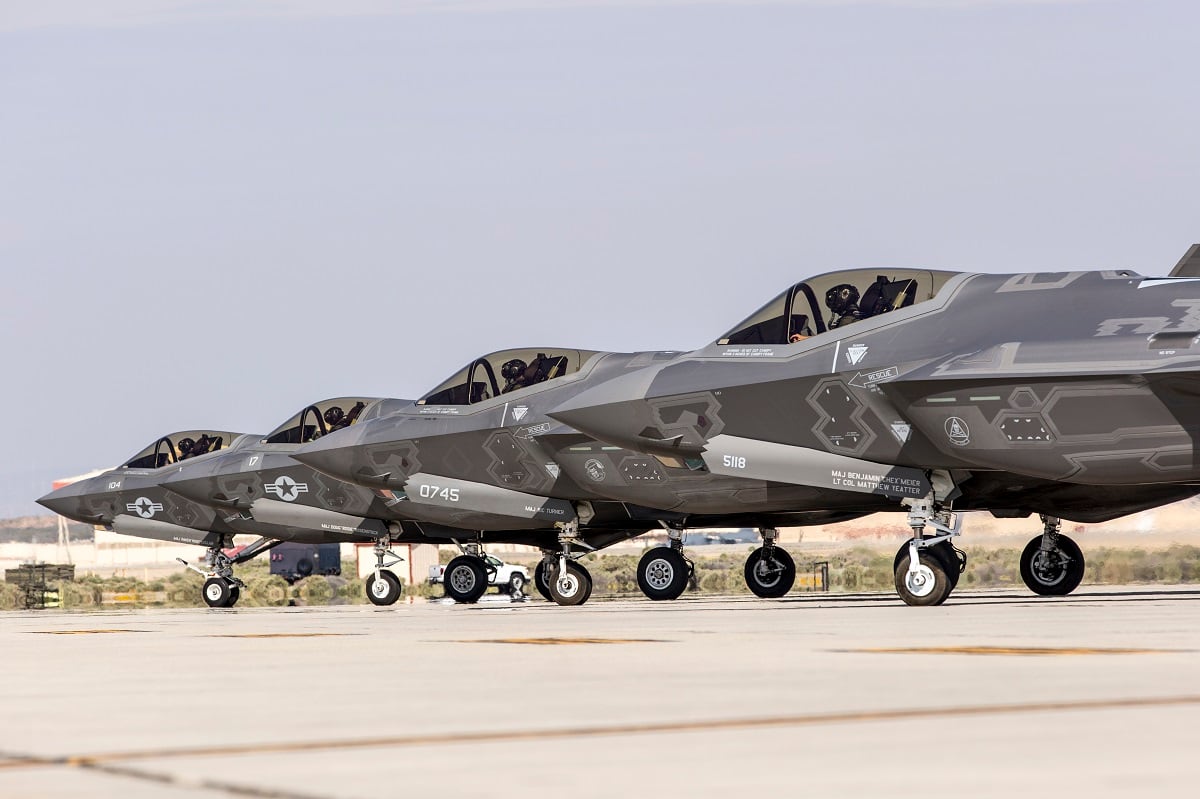
However, still left on the checklist is buying the “last stretch of tooling” necessary to support full-rate production, he said. Lockheed and the F-35 Joint Program Office are still in discussions on a contract for that equipment.
The biggest challenge will be ensuring the raw materials are ready and on the production room floor when it’s time to begin fabricating a new F-35, as well as ensuring the supply base can support both production and sustainment.
“So we’re constantly looking at: Are the lead times appropriate? Do I have enough capacity within the supply chain, and how can I improve that?” he said. “Is there [a] way to resequencing [or] refine our sequence of work? As we go faster, we learn how to go faster — so continuously refining our work instructions.”
2. Follow-on modernization
Once the F-35 is approved for full-rate production, the program will immediately move onto its Block 4 follow-on modernization effort, where the jet will get new sensors, weapons and IT upgrades.
Last September, Vice Adm. Mat Winter, the government’s F-35 program head, announced that Block 4 had been reconceptualized as an agile software development — now known as Continuous Capability Development and Delivery, or C2D2 — where incremental software updates will be created and tested at a faster clip than the more traditional waterfall method.
RELATED
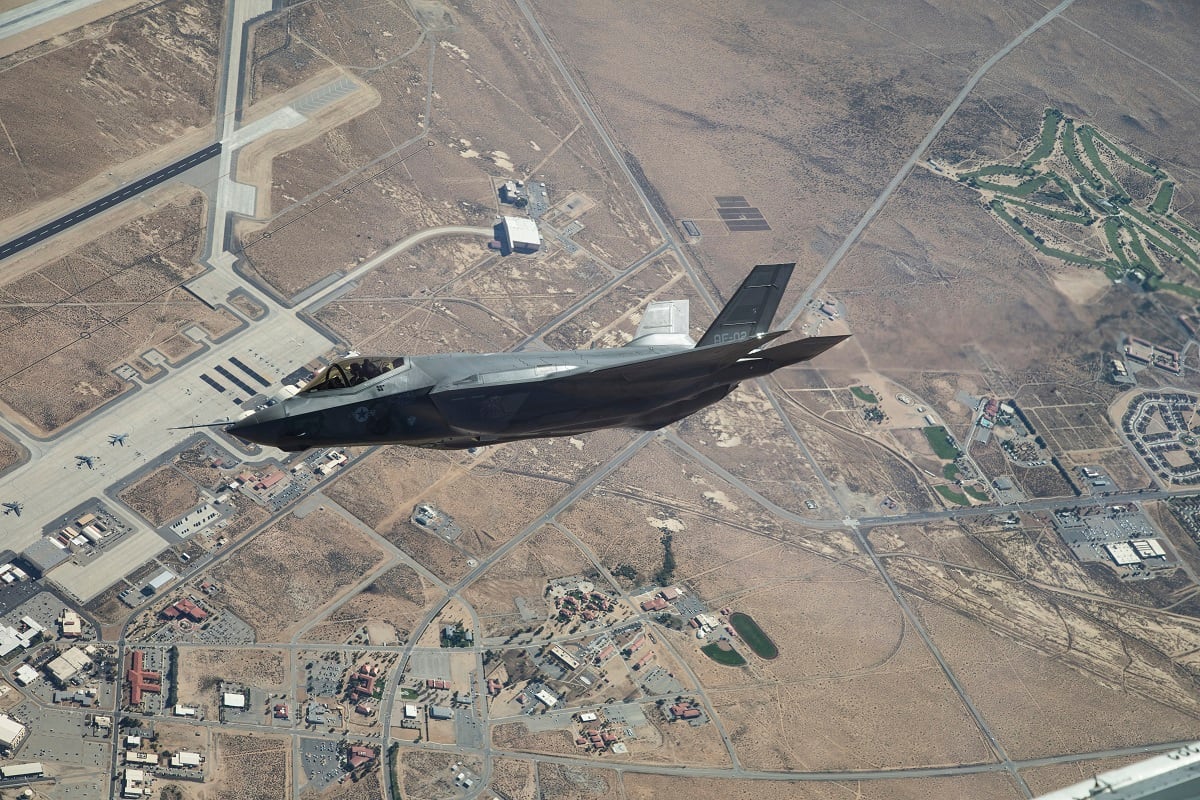
Lockheed has “quite a bit of experience” with agile software development in its Skunk Works technology unit, but less so in its aeronautics business, Ulmer said.
The aeronautics unit has already begun embedding military users within its development cycle, allowing troops to weigh in on a product as it is being created and tested. However, that will need to be more formalized for C2D2, he said.
“That means we’re going to contract different than we are today. We’re going to be a lot more formal with actually bringing the war fighter forward into the development cycle as we do that,” he said. “We’re doing that right now with the JPO, working on those contracting methods.”
Lockheed has engaged the Pentagon’s new software guru, Jeff Boleng, who was named the special assistant for software acquisition in April. Boleng has visited the F-35 production line “a couple times” to get up to speed on the program, Ulmer said.
“Right now he’s trying to learn F-35. It’s that simple. What is our architecture? He’s mentoring both industry and DoD OSD [the Department of Defense’s Office of the Secretary of Defense] relative to the opportunity space that he sees from his experience on how to apply an open-systems architecture [and] how you might restructure that architecture,” he said.
3. Sustainment
As the development phase wraps up, numerous Defense Department officials have voiced concerns about the mammoth costs of sustaining the F-35 throughout its life cycle.
The Pentagon has conveyed that it wants to see at least a 38 percent reduction in sustainment costs by 2036, Ulmer said. While Lockheed isn’t the only company responsible for bringing down cost, it plans to meet its end of the bargain.
“We have projects in place that we are predicting that we are going to meet or exceed that 38 percent reduction over that time period,” he said.
One big push that will help improve sustainability of aircraft is a “technical refresh” for early versions of the Joint Strike Fighter. Jets that were produced in the first six lots of aircraft have poor availability — hovering around 50 percent or less — mostly due to having earlier versions of hardware or subsystems that were less reliable, Ulmer said.
The tech refresh will update older F-35s with new computing tech and improved, more reliable subsystems.
Lockheed has also improved the preventative health onboard maintenance system aboard the aircraft, which tells the user when a part needs to be replaced. Early on, the system would often falsely convey that parts were broken, which drove up sustainment costs and the average time between part failures, Ulmer said.
4. Autonomic Logistics Information System
The F-35’s logistics system — the Autonomic Logistics Information System, or ALIS — has historically been one of the biggest headaches for both Lockheed, which manufactures the product, and the military maintenance community. ALIS used to do everything from mission planning, repairs and the ordering of spare parts, but maintainers have complained about slow speeds and the high number of workarounds needed to use the system.
Over the past 18 months, Lockheed has focused on incremental software upgrades to ALIS that can improve performance, Ulmer said. The company has also sent out Lockheed representatives to a number of military bases — including Marine Corps Air Station Beaufort in South Carolina, Marine Corps Air Station Yuma in Arizona, and Hill Air Force Base in Utah — to get feedback from ALIS users.
“We just sit down with the maintainers and the operators and we learn what are their issues relative to implementation or use of ALIS. Then we rack and stack, in our discussions with them, their priorities. ‘What would you do to improve ALIS operations?’ ”
RELATED
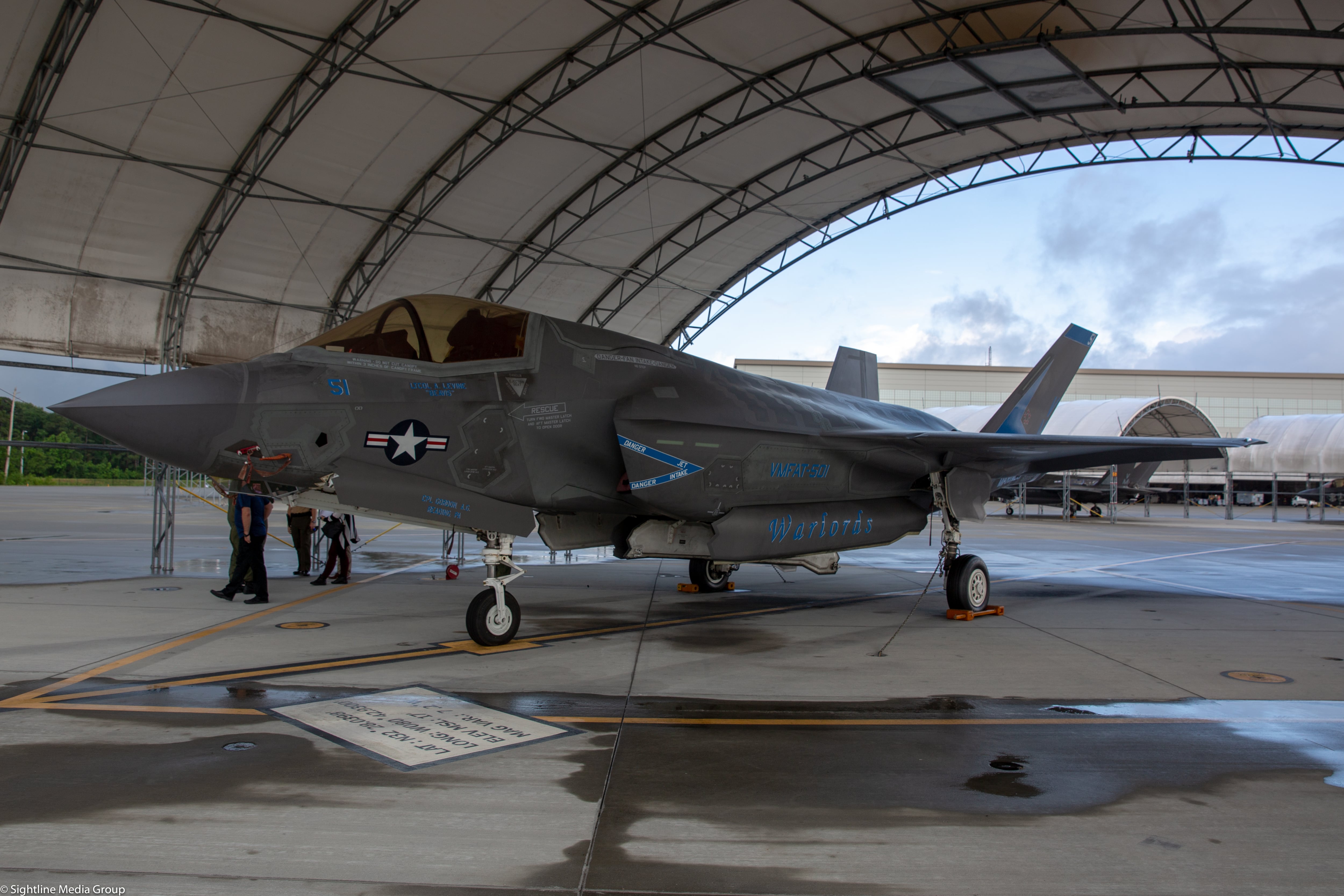
One metric that Ulmer pays attention to is how long it takes for maintainers to register a newly delivered F-35 within the ALIS system.
“We are seeing very good metrics now. Typically within a day or two, that instance has been established and that airplane is flyable,” he said.
But, as Lockheed has been told, it takes too long to re-establish F-35s as part the ALIS system after the jets have been forward deployed.
“Every part on the airplane, ALIS keeps that pedigree with it. So as the airplane ages, that pedigree gets longer and longer and longer, so the data file gets bigger and bigger,” he said. “We’re learning from an architectural point of view you don’t need to carry all of that data with you.”
Valerie Insinna is Defense News' air warfare reporter. She previously worked the Navy/congressional beats for Defense Daily, which followed almost three years as a staff writer for National Defense Magazine. Prior to that, she worked as an editorial assistant for the Tokyo Shimbun’s Washington bureau.