PEARL HARBOR NAVAL SHIPYARD, Hawaii — The U.S. Navy’s westernmost naval shipyard is revamping its processes and its collaboration between departments in a bid to finish more submarine repair work on time, the commanding officer said.
The Pearl Harbor Naval Shipyard and Intermediate Maintenance Facility is fundamentally rethinking what it takes to start and finish maintenance availabilities on time, and is pulling best practices from its three fellow public shipyards, all as part of the Navy’s larger Naval Sustainment System-Shipyards and Performance to Plan efforts, Capt. Richard Jones told Defense News in a visit to the Hawaiian yard.
The shipyard has four dry docks plus pier space to work on submarines and surface ships, whether they’re based in Hawaii and Guam or just passing through the region. Jones said that leads to a complex mix of work: some lengthier depot availabilities and some short-duration, intermediate-level work, but all requiring the same trade shops.
Jones said that as his shipyard team tried to identify how they could improve performance, they realized there was a jumble of communication between the various project teams and shops. A section in the machine shop might start one job and finish it on time, for example, but if the other trades were prioritizing work for a different submarine, then the machinists’ on-time work was for naught, and the priority submarine would still overrun its schedule.
The shipyard has long maintained an integrated schedule of all the various activities taking place to support maintenance availabilities, but it still wasn’t seeing consistent on-time deliveries of submarines and ships. So, Jones said, the yard asked a chicken-or-egg type of question: Could it have a greater effect if personnel focused on starting a maintenance availability on time, or ending on time?
“There is a direct relationship: If you don’t finish the predecessor job on time, then the successor job can’t start on time” because the same personnel move from one project to the next, he said.
So the yard has turned its focus to helping project teams finish strong and complete submarine work on time. “It sounds easy to do,” Jones said, but it’s not: It involves anticipating barriers before they fully reveal themselves, and it involves a lot of communication.
RELATED
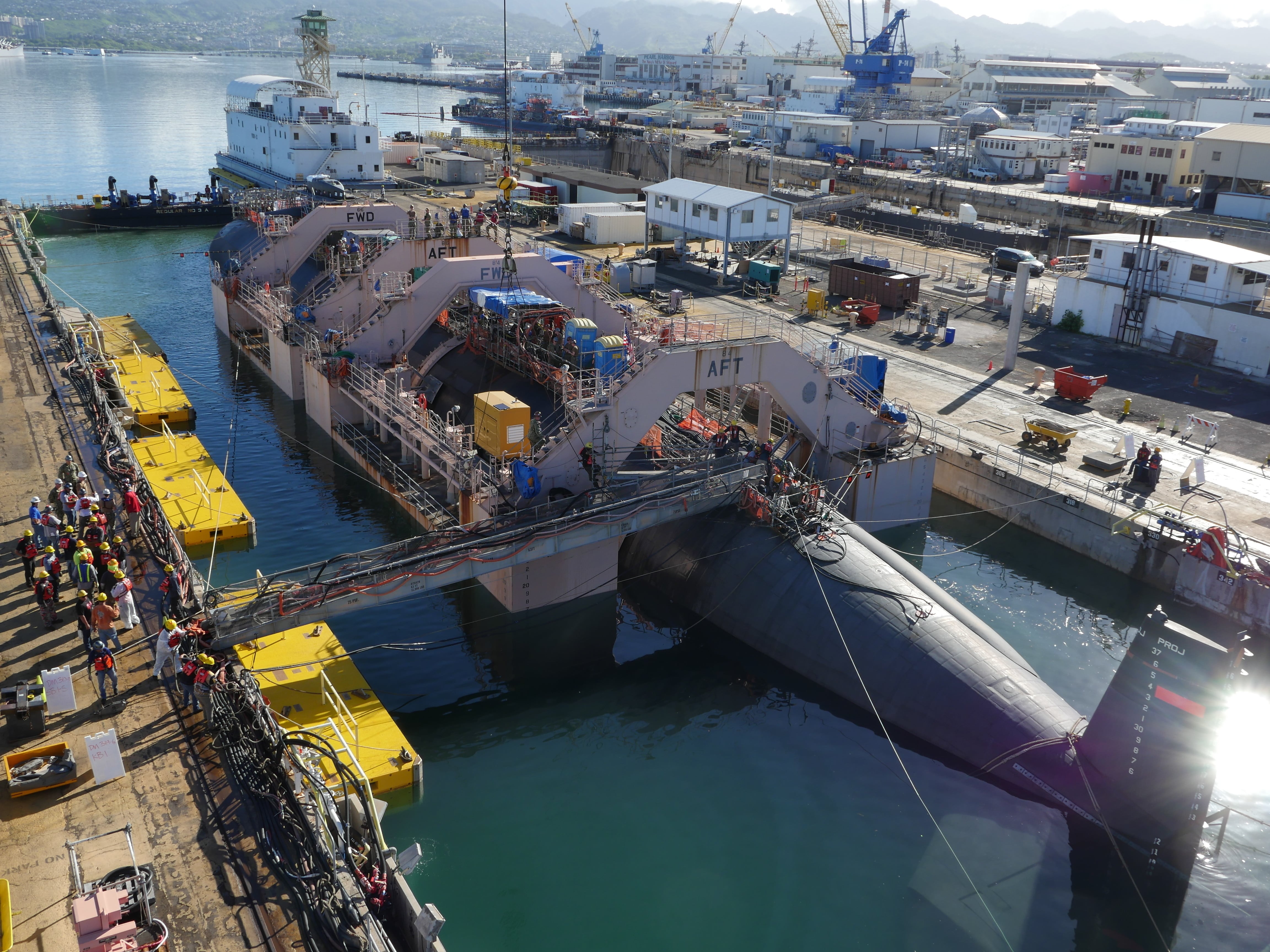
The teams now take it one week at a time: What individual jobs should finish that week? How close are they to completion? What resources could the yard provide to ensure jobs finish on time?
Jones also said there was a cultural factor to overcome, with a pervasive can-do attitude that led people to try to solve a problem on their own even if it meant finishing a job late, versus asking for help so they could finish on time.
One element of Performance to Plan is a “fix or elevate” mindset.
“That’s great to have that can-do attitude, but sometimes you spend so much time trying to do a superhuman effort that you miss all this other work. So now what’s coming is the fix-or-elevate piece: If we can’t fix it in a shorter period of time, then we elevate it up to get help and get more focus on that job,” Jones said.
Jones said the yard is already seeing better performance through the fix-or-elevate strategy, though he could not provide metrics.
He did, however, say the Navy is reconsidering what metrics to track to better understand ship repair performance and identify areas for improvement. Retired Adm. William Lescher, who served as vice chief of naval operations and had spearheaded the Naval Sustainment System-Shipyards and Performance to Plan efforts, visited Pearl Harbor in July to discuss the metrics initiative, Jones added.
The captain also said materials and process instructions were the two biggest barriers to on-time completion, something that has only revealed itself since the yard started pushing the fix-or-elevate mentality.
Material bottlenecks can be harder to tackle. Being on an island in the middle of the ocean, it’s difficult to quickly obtain items that aren’t already on hand. But better transparency about material shortages can help move items from a lower-priority project to a higher-priority one, and it can help the supply departments better understand what must be kept on hand.
But Jones said the engineering one is easier to address, and it may actually influence the future physical design of the yard.

The four public shipyards are in the early stages of the Shipyard Infrastructure Optimization Program, or SIOP, a 20-year effort to modernize tools and redesign facilities’ layouts for more efficient ship maintenance.
Jones hopes the redesigns will bring amenities like lunchrooms closer to the workforce, but he said he’s most focused on bringing the engineering workforce closer to the trade shops and the dry docks. With the engineers writing work instructions, and the tradesmen implementing them, Jones said, the yard could achieve better on-time completion rates if workers could quickly and correctly interpret these instructions — a scenario made more likely if the two teams’ locations are physically closer.
And Jones hopes the shops will be more centrally located for all the dry docks. The Pearl Harbor Naval Shipyard was opened in 1908, and its first dry dock entered service in 1919. The shops were all set up near the original dry dock. But during World War II, when three additional dry docks were constructed, each new one became successively farther from the shops.
Jones said SIOP would only be the fourth time in the yard’s history that the Navy has invested in major improvements to the facilities, so it’s important to think about not only the work the yard is doing today but how the technology could change, and then create a design that won’t quickly become outdated or inefficient.
The Navy has a dedicated SIOP office overseeing the efforts at all four yards — Pearl Harbor; Puget Sound Naval Shipyard and Intermediate Maintenance Facility in Washington; Portsmouth Naval Shipyard in Maine; and Norfolk Naval Shipyard in Virginia.
Some of the earliest SIOP efforts across the four yards will include building new dry docks to replace old ones that, in many cases, will not be able to accommodate the newest submarines and aircraft carriers currently undergoing assembly. At Pearl Harbor, a new dry dock will replace one that is too shallow to work on surface ships and will be too small for the Block V Virginia-class submarines under construction today.
SIOP spokesman Jeff Cunningham told Defense News an environmental review of that dry dock project was underway and would wrap up in fiscal 2023.
Cunningham said all four shipyards completed a modeling and simulation effort to map out workflows at the shipyards, and Pearl Harbor will be the first to translate that information into an area development plan with the proposal for a new, optimized layout.
“Our area development plan aims to improve our shipyard layout such that transit time of parts and materials are reduced while providing modernized facilities for our shipyard employees,” he said. “The [area development plans] will present a long-range investment plan to recapitalize the shipyards” in a way that balances optimizing the renovation schedule while also minimizing disruptions to the ongoing maintenance work that cannot be paused while shops and dry docks are replaced or renovated.
Megan Eckstein is the naval warfare reporter at Defense News. She has covered military news since 2009, with a focus on U.S. Navy and Marine Corps operations, acquisition programs and budgets. She has reported from four geographic fleets and is happiest when she’s filing stories from a ship. Megan is a University of Maryland alumna.